Heat transfer model and finite element formulation for simulation of selective laser melting
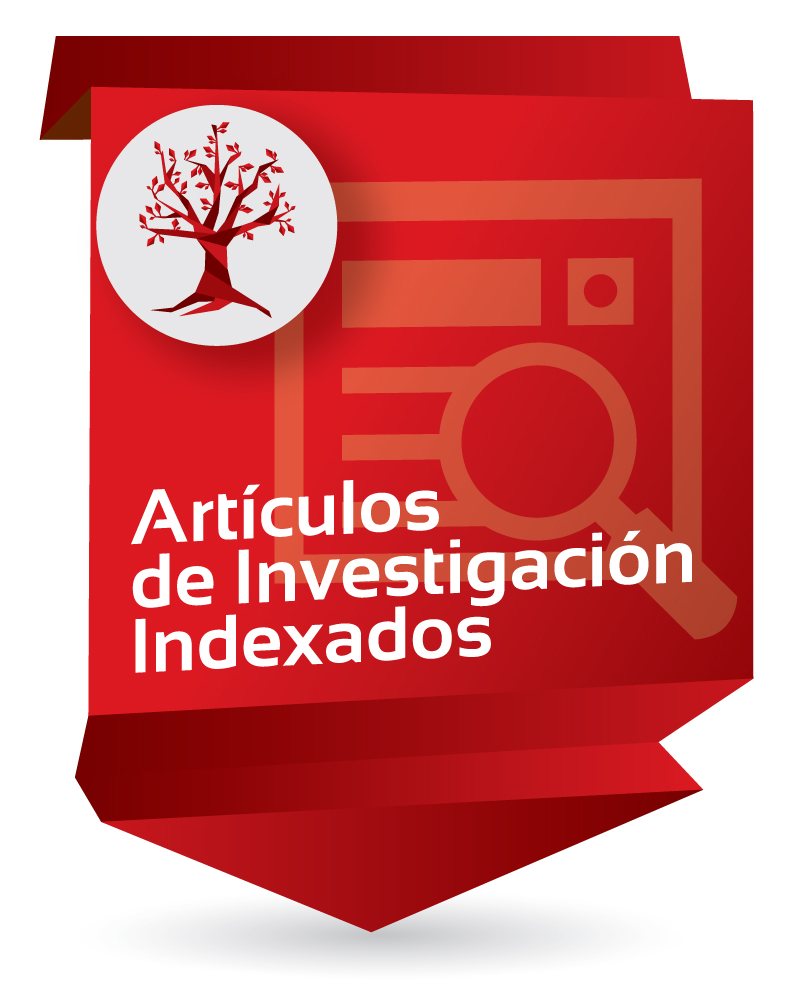
Enlaces del Item
URI: http://hdl.handle.net/10818/37249Visitar enlace: https://link.springer.com/arti ...
Visitar enlace: https://link.springer.com/cont ...
ISSN: 0178-7675
ISSN: 1432-0924
DOI: 10.1007/s00466-017-1496-y
Compartir
Estadísticas
Ver Estadísticas de usoCatalogación bibliográfica
Mostrar el registro completo del ítemFecha
2018-09Resumen
A novel approach and finite element formulation for modeling the melting, consolidation, and re-solidification process that occurs in selective laser melting additive manufacturing is presented. Two state variables are introduced to track the phase (melt/solid) and the degree of consolidation (powder/fully dense). The effect of the consolidation on the absorption of the laser energy into the material as it transforms from a porous powder to a dense melt is considered. A Lagrangian finite element formulation, which solves the governing equations on the unconsolidated reference configuration is derived, which naturally considers the effect of the changing geometry as the powder melts without needing to update the simulation domain. The finite element model is implemented into a general-purpose parallel finite element solver. Results are presented comparing to experimental results in the literature for a single laser track with good agreement. Predictions for a spiral laser pattern are also shown.
Palabras clave
Ubicación
Comput Mech (2018) 62: 273
Colecciones a las que pertenece
- Facultad de Ingeniería [582]